What is a Magnet?
A magnet is a material that exerts obvious force on it without physical contact with other materials. This force is called magnetism. Magnetic force can attract or repel. Most known materials contain some magnetic force, but the magnetic force in these materials is very small. For some materials, the magnetic force is very large, so these materials are called magnets. The earth itself is also a huge magnet.
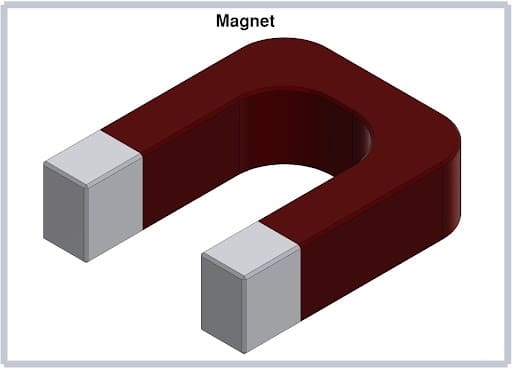
There are two points on all magnets where the magnetic force is greatest. They are known as the poles. On a rectangular bar magnet, the poles are directly across each other. They are called the North Pole or north-seeking pole, and the South Pole or south-seeking.
A magnet can be simply made by taking an existing magnet and rubbing a piece of metal with it. This metal piece being used must be rubbed continuously in one direction. This makes electrons in that metal piece start spinning in the same direction. Electric current is also capable of creating magnets. Since electricity is a flow of electrons, when the mobile electrons move in a wire they carry with them the same effect as electrons spinning around the atomic nucleus. This is called an electromagnet.
Due to the way their electrons are arranged, the metals nickel, cobalt, iron, and steel make very good magnets. These metals can stay magnets forever once they become magnets. Thus carrying the name hard magnets. However these metals and others can behave like magnets temporarily if they have been exposed or come near a hard magnet. Then they carry the name soft magnets.
How Magnetism Works
Magnetism occurs when tiny particles called electrons move in some way. All matter is composed of units called atoms, which in turn are composed of electrons and other particles, which are neutrons and protons. These electrons tend to rotate around the nucleus, which contains the other particles mentioned above. The tiny magnetic force is caused by the rotation of these electrons. In some cases, many electrons in the object rotate in one direction. The result of all these tiny magnetic forces from electrons is a big magnet.
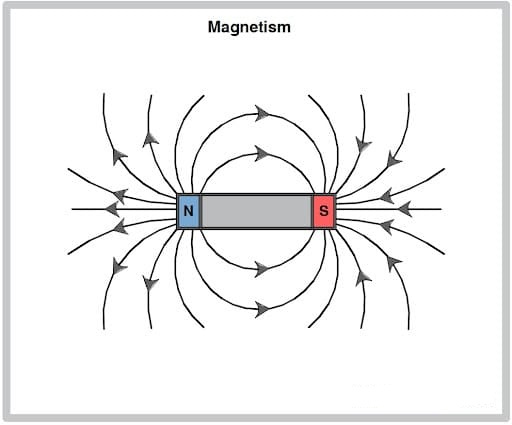
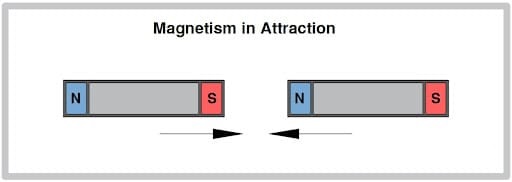
Preparing the Powder
Suitable amounts of iron, boron, and neodymium are heated to melt under a vacuum or in an induction melting furnace using inert gas. The use of the vacuum is to prevent chemical reactions between the melting materials and air. When the molten alloy has cooled, it is broken and crushed forming small metal strips. Afterward, the small pieces are pulverized and crushed into a fine powder which ranges from 3 to 7 microns in diameter. The newly formed powder is highly reactive and is able to cause ignition in air and must be kept away from exposure to oxygen.
Isostatic Compaction
The process of isostatic compaction is also called pressing. The powdered metal is taken and positioned in a mold. This mold is also called a die. In order for the powdered material to be in line with the powder particles a magnetic force is exerted, and during the period the magnetic force is being applied, hydraulic rams are used to compress it wholly to within 0.125 inches (0.32 cm) of its planned thickness. High pressures are used usually from 10,000 psi to 15,000 psi (70 MPa to 100 MPa). Other designs and shapes are manufactured by putting the substances in an airtight evacuated container before pressing them into the desired shape by gas pressure.
Most of the materials taking for example, wood, water, and air have magnetic properties which are very weak. Magnets attract objects that contain the former metals very strongly. They also attract or repel other hard magnets when they are brought closer. This result is because every magnet has two opposite poles. The south poles attract the north poles of other magnets, but they repel other south poles and vice versa.
Manufacturing Magnets
The most common method used in manufacturing magnets is called powder metallurgy. Since magnets comprise different materials, the processes of manufacturing them are also different and unique on their own. For example, electromagnets are made using metal casting techniques, while flexible permanent magnets are manufactured in processes involving plastic extrusion in which raw materials are mixed in heat before being forced through an opening under extreme pressure conditions. Below is the process of magnet manufacturing.
All crucial and important aspects of selection of magnets should be brought under discussion with both engineering and production teams. The magnetizing process on the manufacturing processes of magnets, to this point, the material is a piece of compressed metal. Though it was exerted onto a magnetic force during the process of isostatic pressing, the force did not bring a magnetic effect to the material, it only lined up the loose powder particles. The piece is brought between the poles of a strong electromagnet and afterwards oriented in the direction intended of magnetization. After the electromagnet is energized, the magnetic force aligns the magnetic domains within the material, making the piece a very strong permanent magnet.
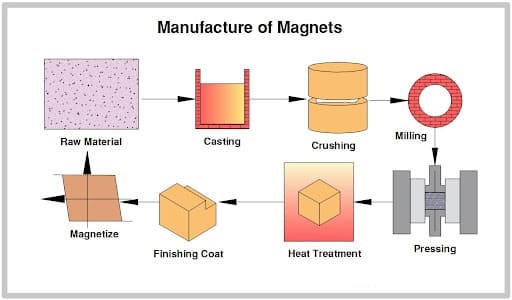
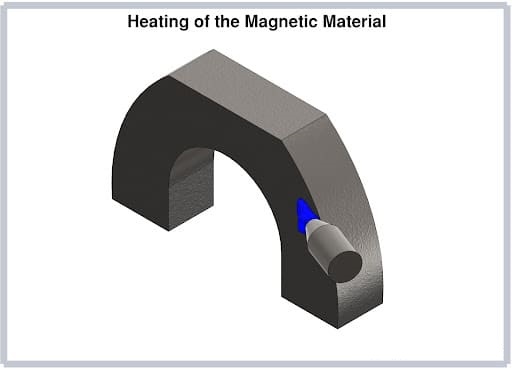
Heating of the Material
After the process of isostatic compaction the slug of the powdered metal is separated from the die and put in an oven. Sintering is the process or method of adding heat to compressed powdered metals in order to transform them into fused, solid metal pieces afterward.
The sintering process mainly comprises three stages. During the initial stage process, the compressed material is heated at very low temperatures in order to drive away all moisture or all the contaminant substances that may have been entrapped during the isostatic compaction process. During the sintering second stage, there is a rise in temperature to about 70-90% of the alloy’s melting point. The temperature is then held there for a space of hours or days in order for the small particles to match, bond and fuse together. The final stage of sintering is when the material is cooled very slowly in controlled temperature increments.
Annealing of the Material
After the heating process comes the process of annealing. This is when the sintered material undergoes another step by step controlled heating and cooling process in order to discard any or all residual stresses that are left within the material and make it stronger.
Magnet Finishing
The above sintered magnets consist of some level or degree of machining, ranging from grinding them smooth and parallel or forming smaller parts out of block magnets. The material making the magnet is very hard and brittle (Rockwell C 57 to 61). Therefore this material needs diamond wheels for the slicing processes, they are also used for abrasive wheels for the grinding processes. The process of slicing can be done with great precision and usually removes the need for the process of grinding. The above mentioned processes require to be done very carefully in order to reduce chipping and cracking.
There are cases where the final magnet structure or shape is very conducive to processing with a shaped diamond grinding wheel like bread loaves. The end result in the final shape is brought past the grinding wheel and the grinding wheel provides accurate and precise dimensions. The annealed product is so close to the finished shape and dimensions that it is desired to be made. Near net shape is the name that is usually given to this condition. A last and final machining process removes any excess material and presents a very smooth surface where needed. Finally in order to seal the surface the material is given a protective coating.
Magnetizing Process
Magnetizing follows the finishing process, and when the manufacturing process is done, the magnet needs charging in order to produce an external magnetic field. To achieve this, solenoid is used. A solenoid is a hollow cylinder into which different magnet sizes and shapes can be placed or with fixtures a solenoid is crafted to impart various magnetic patterns or designs.in order to avoid handling and assembling these powerful magnets in their magnetized conditions large assemblies can be magnetized. Consideration should be done to the magnetizing field requirements, which are very substantial.
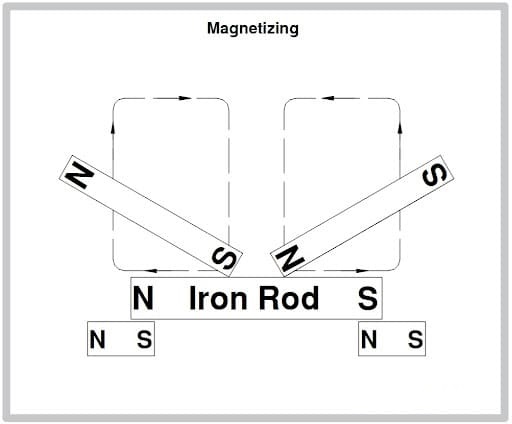
Post time: Jul-05-2022