Sintered Neodymium Iron Boron (NdFeB) Magnets
Sintered Neodymium Magnets is currently one of the most widely used Permanent Magnet Materials in commercial use, with extremely high magnetic energy product and magnetic force. Sintered Neodymium Magnets are composed of rare earth magnetic materials such as neodymium, iron, and boron, which have high coercivity. Sintered Neodymium Magnets is a very high energy density product (up to 55MGOe) with high coercivity. Neodymium Iron Boron Magnets are always used to reduce the size of hard disk drives, motors, and audio devices. Its working temperature can range from 80 ° C to 230 ° C, but high-quality Neodymium Magnetic Materials that can operate above 120 ° C can become very expensive.
However, Sintered NdFeB Magnets have low mechanical strength, are prone to brittleness, and are prone to oxidation due to their iron content, resulting in poor corrosion resistance. Electroplated coatings are usually required, such as nickel plating, epoxy resin coating, and polyxylene coating. Sintered Neodymium Magnets have very strong magnetism and are difficult to demagnetize. Sintered Neodymium Magnets have replaced AlNiCo Magnets and Ferrite Magnets in many applications, including different types of motors in computer hard drives such as magnetic head actuators, magnetic resonance imaging (MRI), speakers, and headphones. Sintered Neodymium Magnets also have outstanding performance in different application fields.
Shapes of Sintered Neodymium Magnets
Sintered Neodymium Magnets can be manufactured into various shapes to suit different purposes. Some common shapes include:
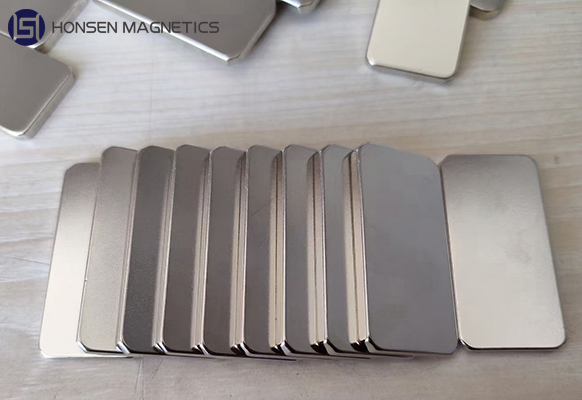
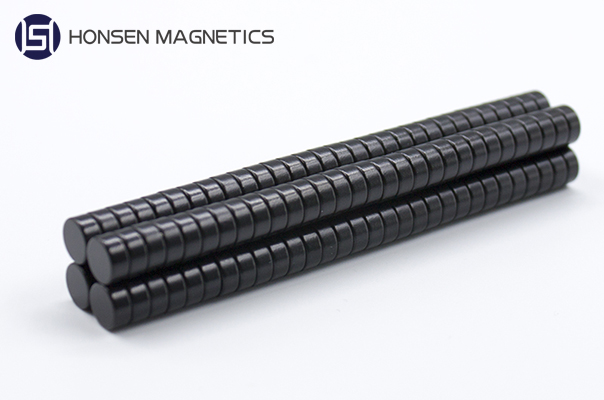
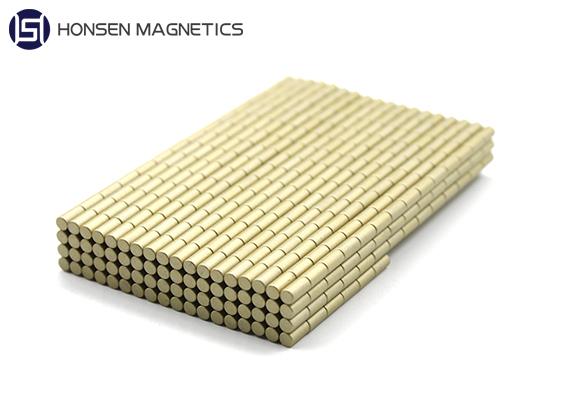
Block / Rectangular: Block Magnets, also named Rectangular Magnets or Squared Magnets, are rectangular in shape and have sharp corners. Block Magnets are commonly used in magnetic separators to separate ferrous materials, magnetic holding devices to securely hold objects in place, and in sophisticated medical devices like magnetic resonance imaging (MRI) machines to generate strong and uniform magnetic fields.
Disc: Disc Magnets with their flat and circular design, are extensively utilized in various industries, particularly in the fields of motors and generators. These compact yet powerful magnets offer efficient magnetic force, allowing for optimal performance and functionality in the machines.
Cylinder: Cylinder Magnets, characterized by their elongated and round shape, are widely used for their unique properties. With its long and circular design, it offers enhanced stability and easy handling. Cylinder Magnets can be found in various industries, such as robotics, automotive, and medicine, where their strong magnetic fields play a crucial role in achieving desired outcomes.
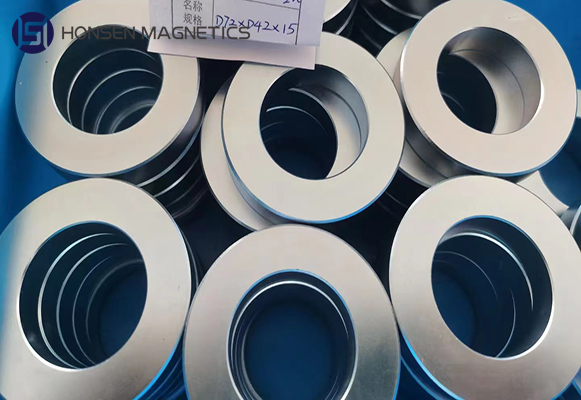
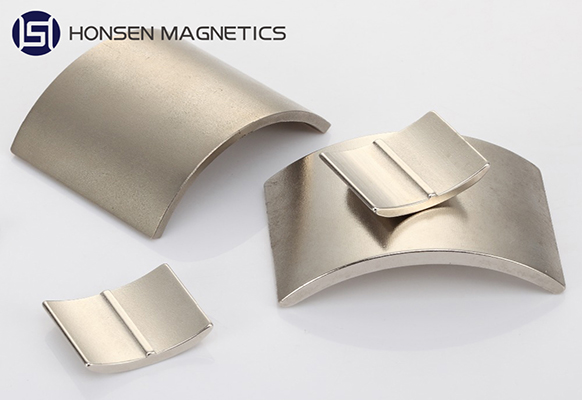
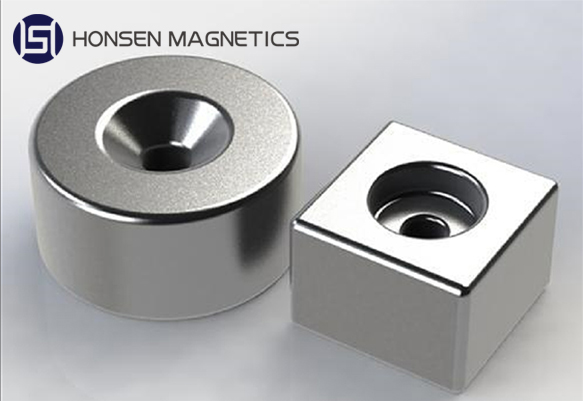
Ring: Ring Magnets have a circular shape with a hole in the center. Their primary utility lies in powering electromechanical contraptions like speakers, microphones, and electric motors. Thanks to their circular shape, ring magnets can produce a uniform and efficient magnetic field, making them invaluable in these applications.
Arc: Arc Magnets also called Segment Magnets, boast a distinctive curved shape reminiscent of a section of a circle. These magnets are highly sought after in a multitude of applications that necessitate a curved magnetic field. Notably, they find extensive use in magnetic sensors, magnetic couplings, motors, and magnetic switches. Their ability to generate a precise and tailored magnetic field makes them invaluable in these industries.
Countersunk: Countersunk Magnets are powerful magnets that have a conical recess allowing them to be easily embedded or flush-mounted into various materials. They are ideal for applications where a sleek and seamless appearance is desired, such as in cabinetry, signage, or DIY projects. With their strong magnetic pull and convenient design, Countersunk Magnets provide a practical and aesthetically pleasing solution for countless applications.
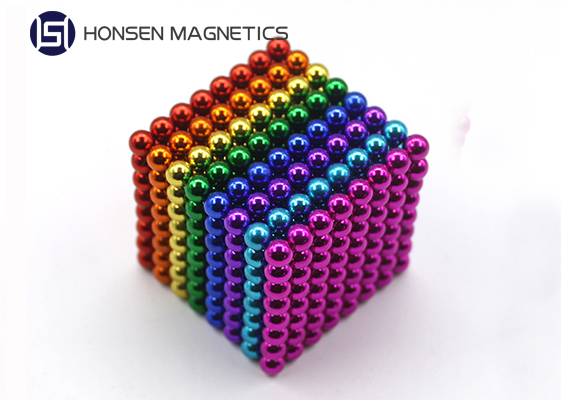
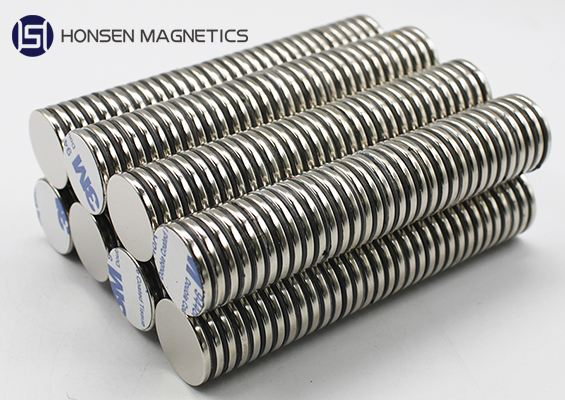
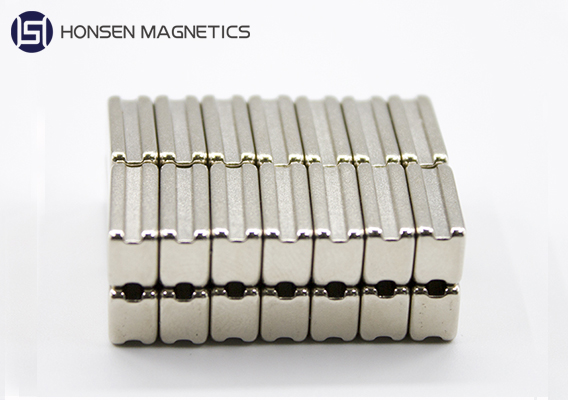
Ball: Ball Magnets, also known as Sphere Magnets, are small spherical objects that possess strong magnetic properties. Ball Magnets are used in various fields including magnetic therapy, where they are used for pain relief and promoting healing. They are also popular in arts and crafts projects, offering endless possibilities for creative endeavors. Scientists also utilize ball magnets in experiments and research, tapping into their unique magnetic properties.
3M Adhesive: 3M Adhesive Magnets are a convenient magnetic solution. They are made of NdFeB Magnets and come with 3M adhesive tape already applied. With their strong magnetic properties and easy-to-use adhesive, these magnets can be quickly and securely attached to various surfaces. Whether for home, office, or DIY projects, they offer a convenient way to display or organize objects without drilling or other installation methods.
Customized shapes: Sintered Neodymium Magnets can also be manufactured into customized shapes to meet specific requirements for particular applications. It's important to note that the shape of the magnet affects its magnetic properties, so the appropriate shape should be chosen based on the intended application and desired magnetic performance.
Manufacturing Process of Sintered Neodymium Magnets
Sintered Neodymium Magnets are typically manufactured using a powder metallurgy process. Micron-sized neodymium iron boron powder is produced in an inert gas atmosphere and then compacted in steel or copper molds, which produces a shape similar to the final product, known as a Green Body. The magnetic properties of Sintered Neodymium Magnets are generated by applying a magnetic field before or during the pressing process. This applied magnetic field gives the Sintered Neodymium Magnets magnetization direction, and the arrangement of particles produces anisotropic magnetism, greatly enhancing the remanence (Br) and other magnetic characteristics of the finished rare earth magnet. The Green Bodies are then placed in vacuum bags, and these Green Bodies are immersed in oil, with the fluid in the vacuum bags pressing on all sides of the Green Bodies, increasing their density, in a process known as isostatic pressing. After the pressing process of isostatic pressing, the Green Body of Sintered Neodymium Magnets are subjected to sintering and heat treatment until they reach a fully dense state. The Green Bodies are then processed into the final required dimensions, and undergo electroplating, magnetization, and packaging, before being shipped to customers.
The production process of Sintered Neodymium Magnets can be summarized as follows:
1. Materials Preparation 2. Smelting 3. Hydrogen Decrepitation 4. Jet Milling 5. Mold and Isostatic Pressing
6. Sintering 7. Annealing 8. Machining 9. Coating 10. Testing 11. Magnetizing 12. Packing 13. Transportation
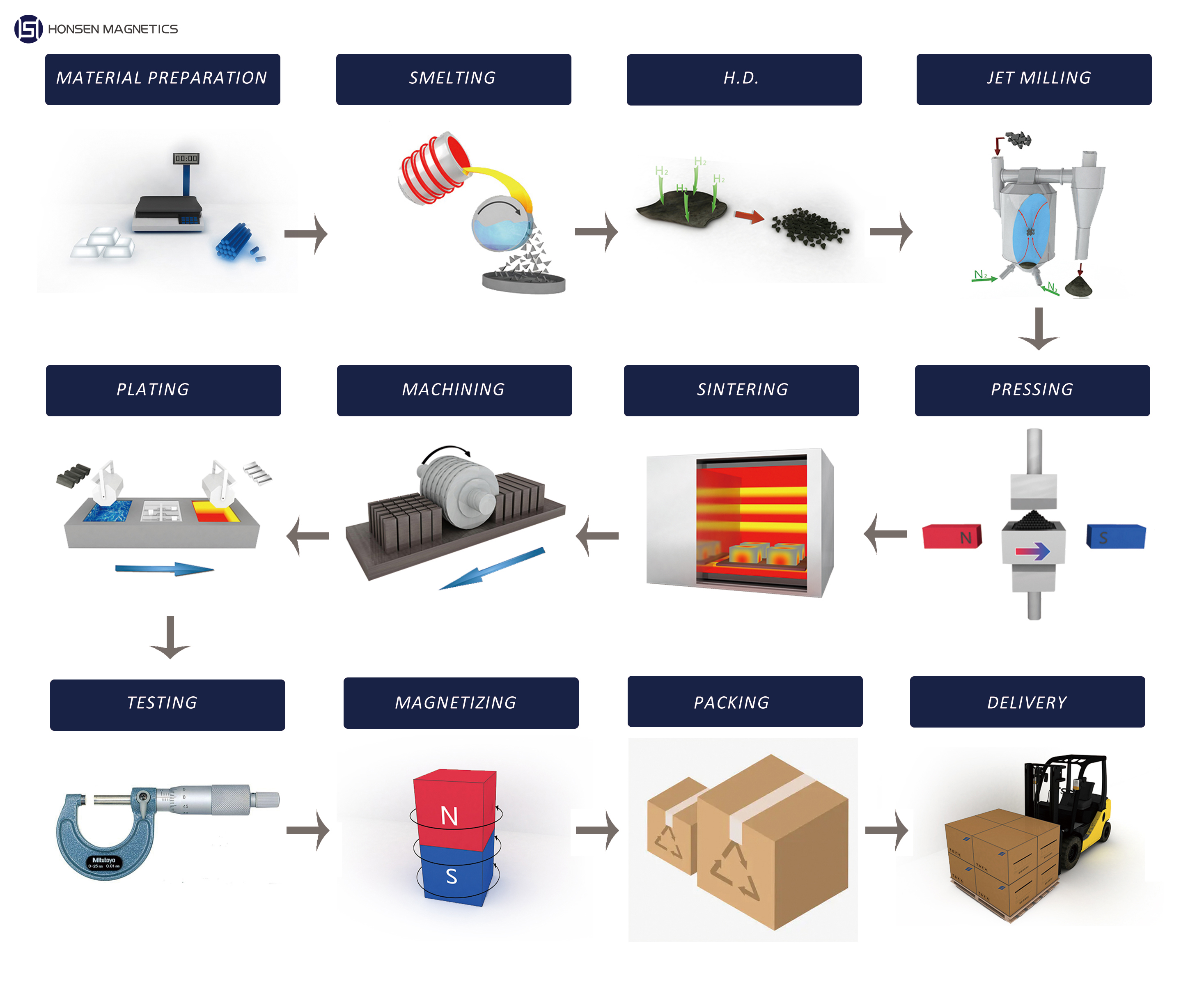
Surface Treatment of Sintered Neodymium Magnets
Surface treatment of Sintered Neodymium Magnets is an important step in the production process. The purpose of surface treatment is to protect the magnets from corrosion and improve their mechanical and magnetic properties. The common surface treatment method is coating the magnets with a layer of protective material. This can be done through processes such as electroplating, epoxy coating, or nickel-copper-nickel (NiCuNi) plating. These coatings provide a barrier against moisture and other environmental factors, preventing the magnets from oxidizing or corroding.
Surface treatment of Sintered Neodymium Magnets plays a vital role in enhancing the performance and longevity of sintered neodymium magnets. By choosing the appropriate coating and magnetization methods, manufacturers can ensure that the magnets meet the specific requirements of their applications, whether it is in the automotive industry, consumer electronics, or renewable energy technologies.
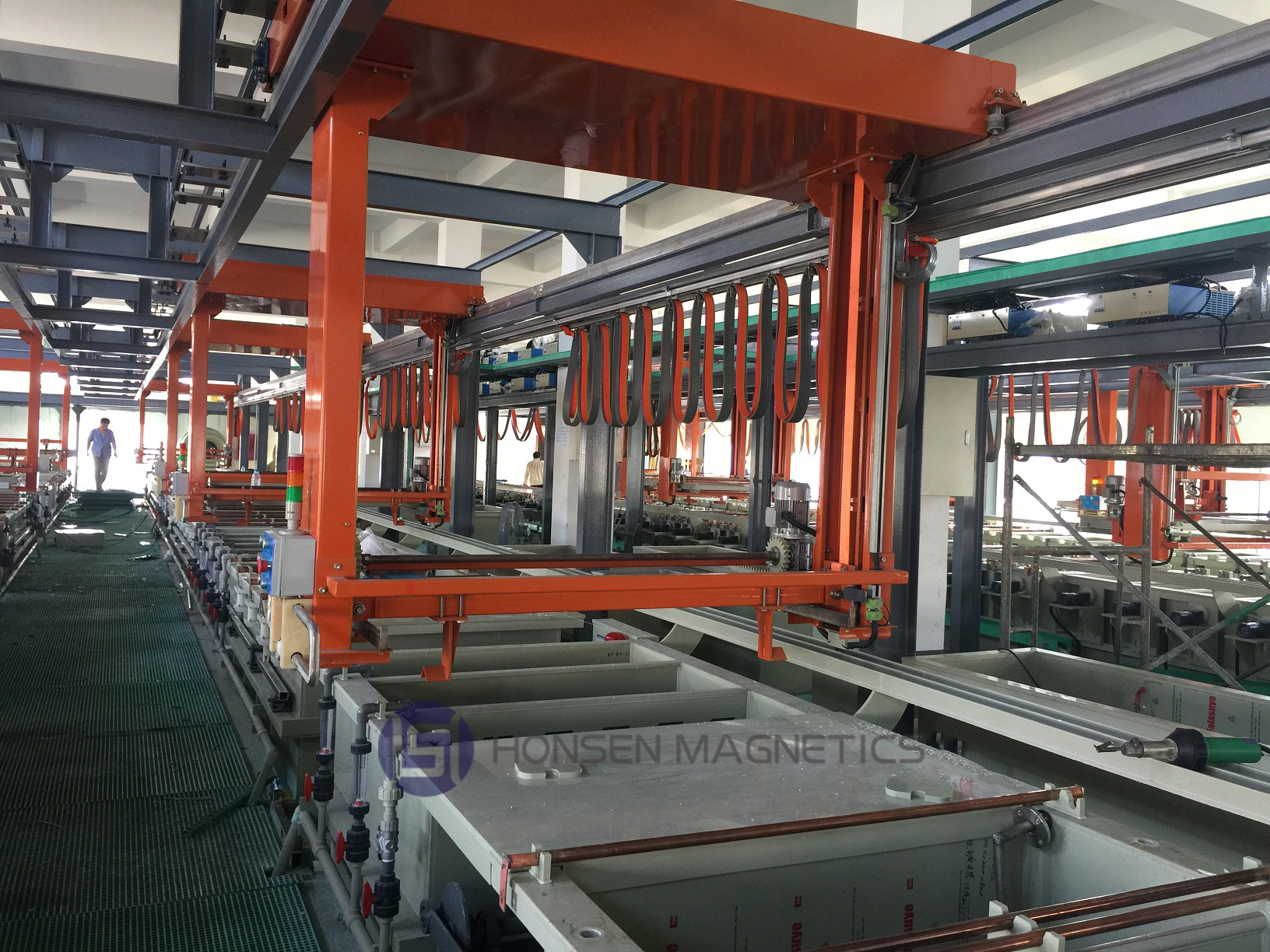
Applications of Sintered Neodymium Magnets
As Sintered Neodymium Magnets are so strong, their uses are versatile. They are produced for both commercial and industrial needs. For example, something as simple as a piece of magnetic jewelry uses a neo to keep the earring in place. At the same time, Sintered Neodymium Magnets are being sent into space to help collect dust from the surface of Mars. Sintered Neodymium Magnets’ dynamic capabilities have even led to them being used in experimental levitation devices. In addition, Sintered Neodymium Magnets are used in such applications as Servo Motors, Magnetic Separators, Magnetic Couplings, Magnetic Rotors, welding clamps, oil filters, geocaching, mounting tools, costumes, and many more.
Honsen Magnetics produces custom Sintered Neodymium NdFeB Magnets and custom Magnetic Assemblies so we can help you find the best fit for your project. Honsen Magnetics has specialized in the production of magnetic materials and has focused on permanent magnets, magnetic components, magnetic assemblies, and its applications for many years. With years of production and R&D experiences, we continue to provide customers with the best quality products and the most cost-effective solutions. Contact us to provide services for your projects.
Magnetic Properties of Sintered Neodymium Magnets
Physical Properties of Sintered Neodymium Magnets
Production Flow of Sintered Neodymium Magnets
WHY CHOOSE US
From the beginning of our establishment, we have always placed utmost importance on the quality of our products. Our relentless dedication to improving both our products and production processes ensures that you will receive the highest quality products. This is not just a claim but a commitment we uphold every day. Our team consists of experienced professionals who excel at every stage of production.
To guarantee exceptional product and process quality, we utilize Advanced Product Quality Planning (APQP) and Statistical Process Control (SPC) systems. These systems diligently monitor and manage conditions during critical manufacturing stages, providing us with the ability to deliver outstanding products consistently. We continuously strive for improvement and implement stringent quality control measures to stand by our promise of providing you with the best products available.
With our skilled workforce and robust quality management systems, we are confident in our ability to consistently meet and surpass your expectations. Our ultimate goal is your satisfaction with the high-quality products we offer.
OUR ADVANTAGES
- More than 10 years of experience in the permanent magnetic products industry
- Over 5000m2 factory is equipped with 200 advanced Machines
- Have a strong R&D team can provide perfect OEM&ODM service
- Have the certificate of ISO 9001, IATF 16949, ISO14001, ISO45001, REACH, and RoHs
- Strategic cooperation with the top 3 rare blank factories for raw materials
- High rate of automation in Production & Inspection
- Pursuing product consistency
- We only export qualified products to customers
- 24-hour online service with first-time response
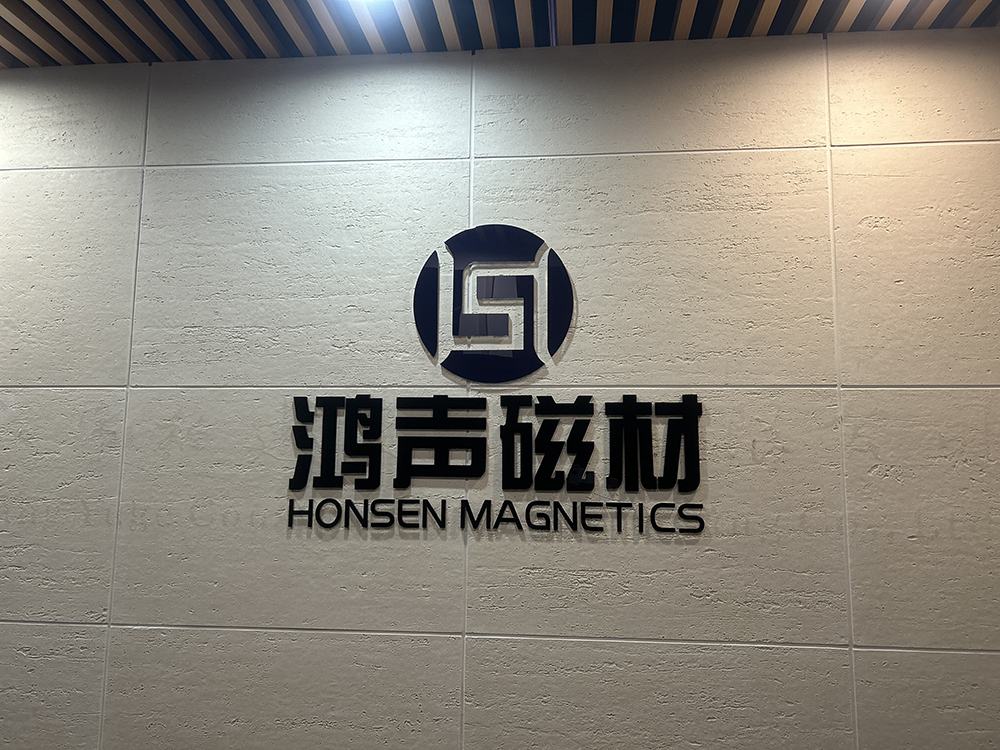
PRODUCTION FACILITIES
With a history of more than ten years, Honsen Magnetics has become a pre-eminent force in the production and distribution of permanent magnets, magnetic components, and magnetic goods. Our skilled team has over a decade of expertise driving a holistic production process covering machining, assembly, welding, and injection molding. This strong infrastructure enables us to offer a wide range of products and has made significant inroads in the European and US markets. Our unwavering commitment to quality, coupled with competitive pricing, has forged deep-rooted relationships resulting in a large and satisfied customer base. At Honsen Magnetics, we take magnetic challenges and turn them into opportunities, redefining industries with every magnet we make.

QUALITY & SAFETY
Quality management lies at the core of our organization, forming the foundation on which we thrive. At Honsen Magnetics we firmly believe that quality is not merely a theoretical construct; it is the driving force behind every decision and action we take.
Our unwavering commitment to excellence manifests in all aspects of our operations. We have adopted a comprehensive approach to quality management, seamlessly incorporating it into every facet of our organization. This holistic integration ensures that quality is not an afterthought but an inherent aspect of our processes and products. From raw materials procurement to production and customer service, our quality management system permeates every stage. Our paramount goal is to consistently surpass the expectations of our customers. By adhering to stringent quality control measures and leveraging cutting-edge technology, we meticulously craft products of unrivaled excellence. Our dedication to exceeding customer expectations is not a mere statement but woven into the fabric of our organization.
Our success hinges on our unwavering dedication to quality management. By integrating it seamlessly into our operations, we consistently deliver exceptional products that reflect our steadfast commitment to excellence.

PACKING & DELIVERY

TEAM & CUSTOMERS
At Honsen Magnetics, we understand that our ability to meet customer needs and maintain excellent safety standards is essential for our success. However, our commitment to perfection extends beyond these aspects. We also place high priority on the personal development of our workforce.
We foster a nurturing environment that encourages our employees to grow both professionally and personally. We provide them with various opportunities for training, skill enhancement, and career advancement.
Our aim is to empower our workforce to reach their full potential. We recognize that investing in their personal growth is crucial for achieving long-term success. As individuals within our organization enhance their skills and knowledge, they become more valuable assets, thereby contributing to the overall strength and competitiveness of our business.
By emphasizing personal development within our workforce, we not only establish a strong foundation for our enduring success but also cultivate a culture of continuous improvement. Our commitment to customer satisfaction and safety is complemented by our dedication to fostering the growth and development of our employees. These values serve as the cornerstone of our business.
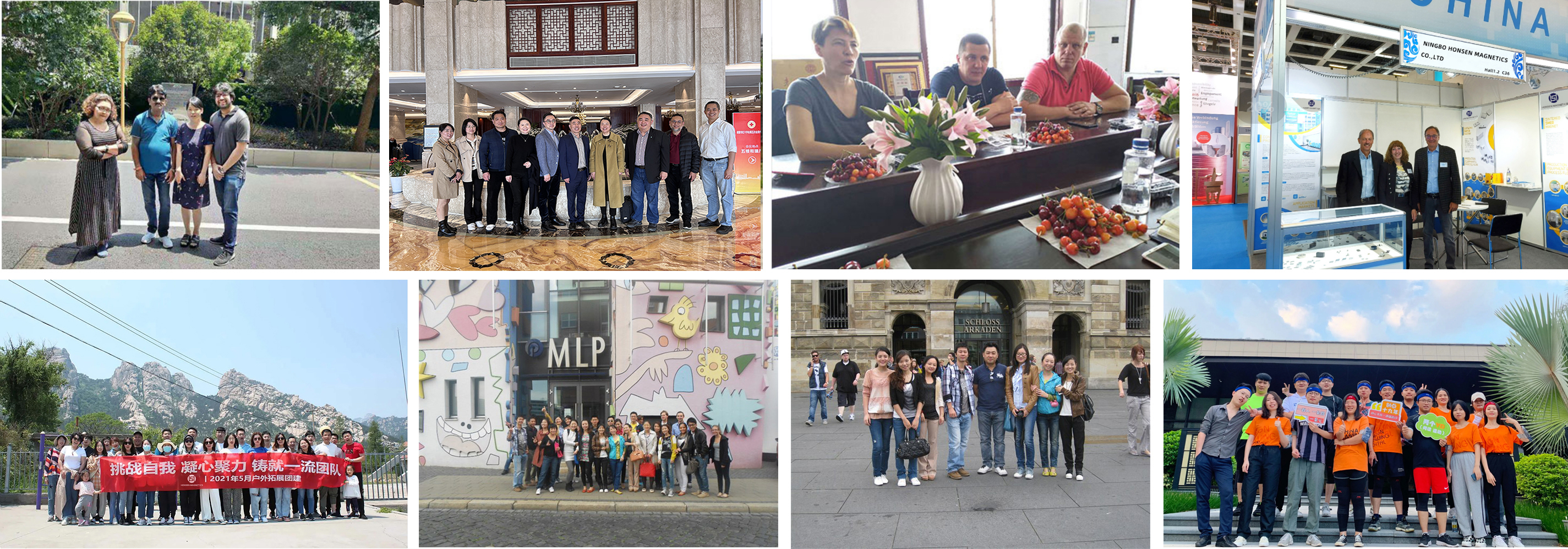
CUSTOMERS' FEEDBACK
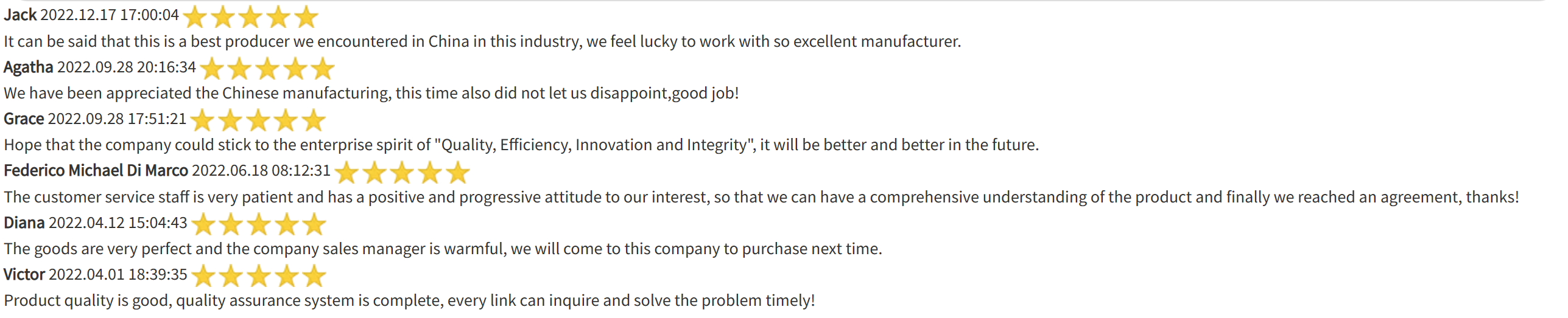